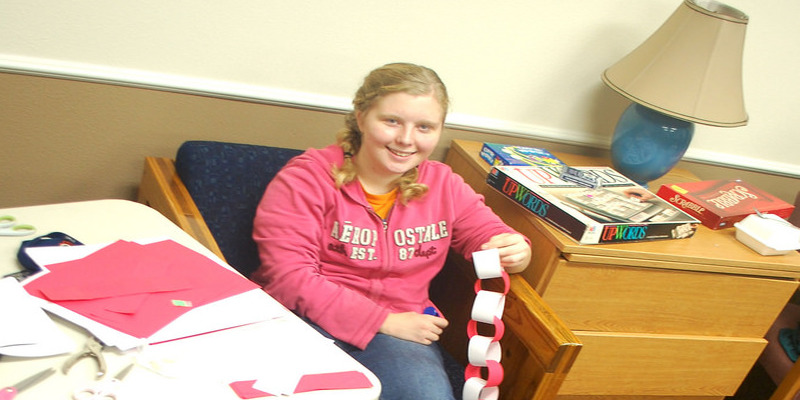
It is no secret that crisp breezes and falling leaves are just around the corner, brushing you toward the cupboard to select your favourite cardigan. Soon this movement will become routine, and scarves and coats will probably be added to the mix.
Personally, it’s pretty uncommon for me to get these things back in their hangers. My guess is because it requires extra work and setting everything on the table or floor just seems simpler: I’m going to wear it again soon, so why not? Well, because soon these piles become hills, and these mountains provide nothing but wrinkled sweaters and missing scarves. I needed a solution.
What I needed were hooks. Hooks in every room and walkway that gathered these piles. But I also needed them to look great. So out came my printing supplies and also a table saw and I had enough timber to create as many racks as I desired.
Because I hear similar complaints rather frequently, I thought it’d be interesting to perform some block-printed rack tutorial. It only takes about 4-5 hours and may be done in tiny steps, making it the perfect post-work project. Give this DIY coat hook a try and reveal your results at the Comments section!
Erin Lang Norris
This is a picture of the completed project so that you know what the final result will look like. I left this one vertical but you can always do a horizontal one instead!
Materials:
Acrylic paint
Block printing ink
Rubber block
Piece of plexiglass or glass
Wood- craft plywood is your most budget friendly
Hooks
Screws for hooks
Sawtooth hangers
Tracing newspaper
Marker
Pencil
Supplies:
Brayer (roller)
Carving tool
Yard stick
Hammer
Utility knife
Drill
Screws
Cotton swabs
Paper towels
Matte finishing spray
Dimensions: 1/4″ piece of timber cut to 8″ x 22″
Approximate price: $25
Erin Lang Norris
The very first step toward creating your own block print is to come up with a layout. Since I have gone through the whole trial and error thing, I figured I will share my 2 cents and hopefully keep you from getting stuck.
My first suggestion would be to use a mark with a bold suggestion when drawing your design. Working with daring marker lines is much simpler than brittle pencil traces.
My other suggestion is to create a shape that’s asymmetrical. It took me a long time to figure out this one and I left myself crazy trying to line up everything perfectly when printing. Simple shapes that are organic and asymmetrical are much more forgiving.
Erin Lang Norris
Once you have a layout you prefer, you may use a backup machine to re-size it if needed. I find this especially useful if you want to make a print that’s fairly large. In my instance, I scaled my own drawing 90% so the repeating pattern could fit better on the timber I had cut.
Next you can use a pencil to duplicate your design on tracing paper. After I took this picture, I went over my lines again to make them heavier. Now, you’re preparing to move your design on rubber so that you want to make confident the graphite will readily shift to its surface.
Erin Lang Norris
Now it’s time to move. Twist your tracing paper upside down so that your pencil marks touch with the rubber. Use the corners of the rubber to your benefit so that you merely need to cut two sides once you remove the additional rubber.
Erin Lang Norris
Next it’s time to cut. If this is the first time dividing, I strongly suggest practicing on another piece of rubber first. This area of the project tends to take the most patience. I suggest walking away for a bit if you feel like you need to.
As soon as you finish cutting, trim the edges to create the look as centered as possible. Leave a perimeter between the Plan and the edge of the rubber.
Erin Lang Norris
So now your block is all carved and you have made sure the negative distances are gouged out so they do not hold onto any undesirable ink. I always do a test print at this point using a very small amount of ink.
This really is a great time to practice rolling ink. Roll it out until you’ve got a thin, even layer of ink. This component can take a little while. Next, roll it on the rubber as thinly as possible.
Erin Lang Norris
Turning the rubber upside down, carefully place it on the newspaper and then apply pressure with your palm or fingers. Press firmly enough to move the ink, but not so hard that you feel like you’re smashing it. After you press a few times, you’re able to slowly pull off the block. Currently the test print is complete. Now you want to try to find any undesirable ink lines and then split away them while your block is still inked so that you do not miss any spots.
Erin Lang Norris
When you’re delighted with your block, create a hash mark at the center of all four sides. This will aid with alignment if you print. Do the same in your timber.
Notice: I really don’t have a photo of the wood-cutting measure, but basically it’s possible to create yours any size you want and paint it any colour you want. Mine is white and measures about 8″ x 22″. Word of caution: White is catchy because it shows ink smudges.
Erin Lang Norris
By now everything is measured out and you feel great about starting the printing process. This is actually the part that you need to work slightly efficiently so that your ink doesn’t dry. You can use an ink retardant to slow dry times. As for me, I prefer to combine my ink to a colour I enjoy with a putty knife and put a drinking glass over it to keep it from drying. Roll a thin layer of ink and get ready to go.
Erin Lang Norris
Utilizing my marks as a guide, I always start in the center and work my way out so I may have a direct line to work with throughout the project. When I put the block on the timber, I set the border of the block right up to one I printed. This ensures equal spacing across the entire board.
Be careful not to smudge the drying ink if you are printing! If you realize that you are getting ink in places you do not want it, a damp cotton swab can get this up.
Erin Lang Norris
And exhale: printing is finished! I have printed almost 100 of those things (some on a much smaller scale) and I will say that though it becomes easier over time, I get worried throughout the entire printing process, but I love doing this.
You need to work fast, and I discover I must wash off my block and brayer a few times during the process because the ink becomes gunky. As I mentioned previously, this may be alleviated a little bit by means of an ink retardant. Either way, if you discover you need to wash your things, make sure that your tools are completely dry before you resume.
Erin Lang Norris
Once the ink is dry, which may take awhile, you may use a matte spray finish over it so nothing smudges. Since the ink is the most likely water-based, it may smear if it becomes wet from the long run.
When it’s dry, add the hangers on the trunk and measure the spacing for the hooks.
One suggestion I have is to put the hook on the board, make sure it’s level, and use and awl to create a mark at the center of the holes. Then you will have a wonderful anchoring point when you pre-drill your screw holes. Attach the hooks and you’ve got a rack. Yay!
Erin Lang Norris
I thought I’d add a few different racks I have made only so that you may see a variation of the theme. I left this one about four decades back.
Erin Lang Norris
This rack is not block published but it’s painted rather.
Erin Lang Norris
I have this stand in my hall along with the things on it appear to rotate quite often. The background is stained, and the circles are painted. This one took awhile but I really enjoy how it turned out.
More inspiring DIYs:
How to Recover a Seat Cushion
50 Clever DIY Suggestions
Switch Your Carport Into an Outdoor Living Room